Waste for warmth
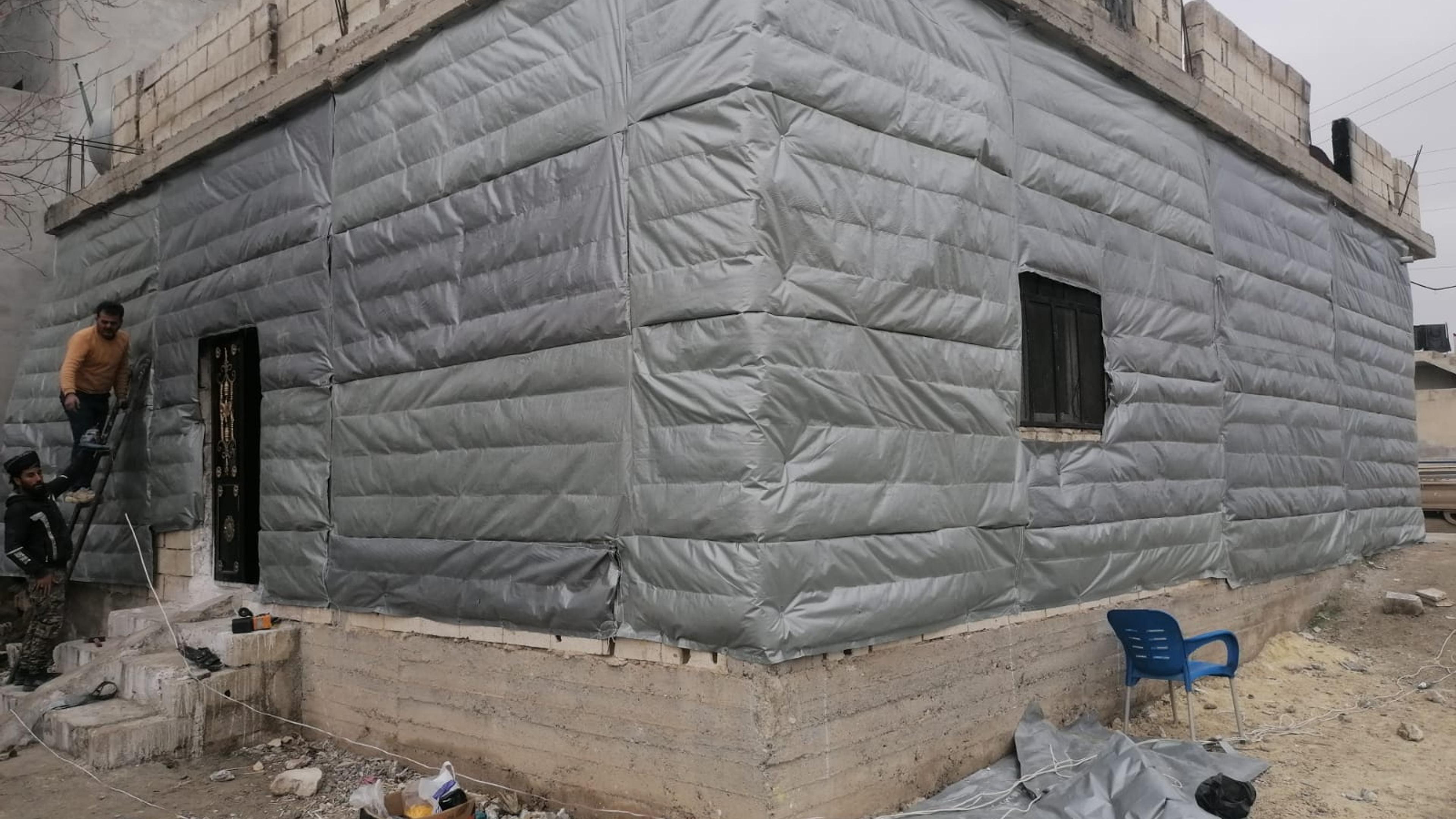
Scope of the project
Millions of displaced people are living in temporary shelters across the Middle East. Among the many challenges they face, is a lack of protection against harsh winters. For those living in camps, existing shelter heating solutions are costly and energy intensive and options to insulate tents are expensive. Current approaches to winterization assistance rely on distribution of blankets, stoves and fuel, and insulation and weather proofing of shelters.
Engineers Without Borders Norway together with its consortium partners Field Ready, Polyfloss Factory and IFRC Shelter Research Unit joined forces to develop and test a new approach to shelter winterisation by making tent insulation from plastic waste. The insulation material is created from recycled plastic by utilizing a technology called Polyfloss. Polyfloss is a mass of thin fibres of plastic that resembles candy-floss in appearance. The fibres can be packed, shaped and formed and it traps air between its fibres, giving it insulating properties. Polyfloss machines can be deployed on-site where the insulation is needed.
The objective was to demonstrate the value of this new, more cost-effective and environmentally sound approach by insulating shelters to help refugees through the cold winter. The project partners also wanted to investigate how this approach could contribute to livelihood opportunities for refugees.
Impact and lessons learned
The primary outcome of the Innovation Lab phase has been the refinement of the Polyfloss machine, allowing it to operate faster and more efficiently and the development of a minimum viable product, a Polyfloss insulation panel. These outcomes have placed the project in an ideal position to transition to the scaling phase.
In terms of results for the end-users of the solutions, direct beneficiary impact in livelihoods is limited to job opportunities. For the first small scale manufacturing pilot that was operated in Gaziantep. From June through August 2021, six people were employed, and from November 1st through the 31st of December five people were employed. These workers operated the Polyfloss machine and manufactured insulation panels. The insulation panels produced in Gaziantep were installed in 13 shelters (approximately 65 people) in North-western Syria.
Preliminary feedback from recipients of the panels is positive, with one sharing, “after my house was insulated with these panels, I felt warm inside and started to turn off the heater in the evening.” While the data is incomplete from the pilot in Syria, it is anticipated that families saw an increase in indoor temperatures during the occasional colder weather patterns and that they were able to reduce their fuel consumption and costs for heating.
The Waste4Warmth project has achieved several objectives and targets set out at the start of the project, however, the reality of implementing a humanitarian innovation program rendered some of the project’s original objectives and targets unrealistic. Where the project was perhaps too ambitious in our objectives was the “tangible impact made in the field.”
Product development of both the insulation products and the machine was time consuming. COVID-19 restrictions placed additional challenges in gathering in-person where significant advances can be realized with multiple people working together and tackling a design challenge. Despite these challenges by the end of the Innovation Lab phase the Waste4Warmth project successfully piloted a small manufacturing operation that saw insulation panels installed on shelters in Syria, this impact was smaller than originally anticipated, but still an important milestone for the project.
The way forward
Additional product development remains as the project continues with further fire testing that will ideally demonstrate that the insulation panel is safe for use on tent shelters. Until that fire testing is concluded the Waste4Warmth project will continue the Scaling phase of the project by pursuing partnerships and further pilots that focus on insulating non-tent shelters, which are also in great need of insulation. Due to their exterior surface types, initial fire testing has concluded the insulation panel is appropriate for use on non-tent shelters.
Transition into the Scaling phase will also see shifts in the project’s partnerships. In the Innovation Lab phase, the priority of the project was machine modification to better serve the humanitarian context. Much time and attention were devoted to working with the Polyfloss Factory, the private sector partner in the Waste4Warmth project to develop the necessary machine modifications. In the Scaling phase there will be a shift in attention to the field partner, Field Ready Turkey, who will be responsible for networking with humanitarian actors operating out of Gaziantep and identifying suitable partnerships for scaling. At the end of the Innovation Lab phase a Waste4Warmth research and development lab was established in Gaziantep that is managed and overseen by Field Ready Turkey. The Polyfloss Factory remains an active project partner in the Scaling phase, but primarily will serve as machine provider while providing some insight and guidance on product development.
Who are the project partners?
Waste for warmth is a partnership between Engineers Without Borders Norway, Field Ready and The Polyfloss Factory.