From waste to value - plastic in humanitarian settings
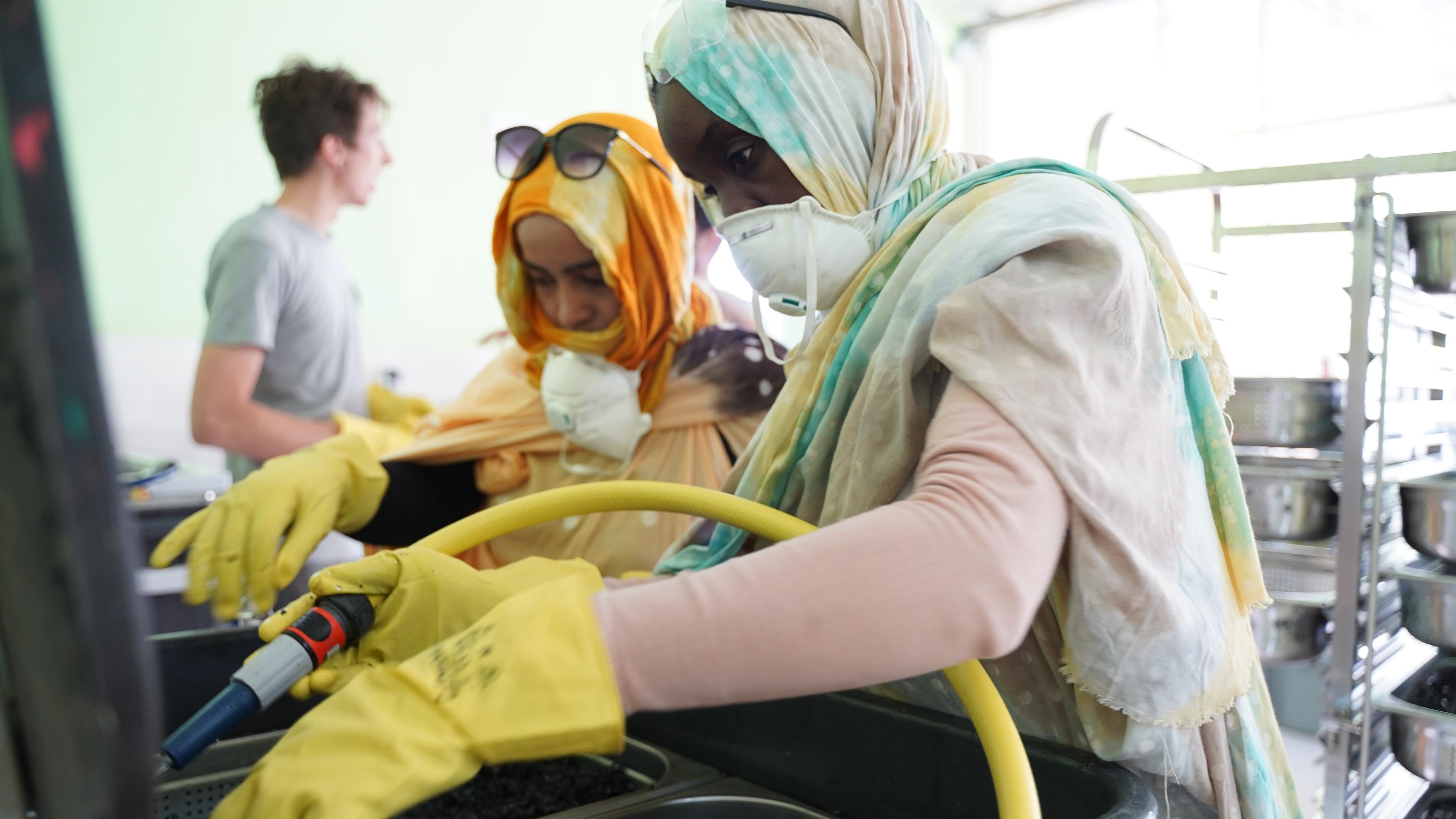
What is the humanitarian challenge?
Sahrawi refugees have been living in a protracted displacement situation in five camps near Tindouf, Algeria for nearly 44 years. Approximately 8.1 million tonnes of waste is generated in these refugee camps annually. A significant amount of this waste is plastic. It is estimated that over 1700 tonnes per year is plastic waste, most of it recyclable. As waste collection services are underfunded and there is no recycling facility, plastic has flooded the streets and the surroundings of the camps, creating many problems.
What is innovative about this project?
Through this project, UNHCR aims to tackle the plastic waste issue through the establishment of systems for improved plastic waste management in five refugee camps in Tindouf, Algeria and create additional income sources for refugees and hosting communities. The project is innovative because it will change UNHCR’s traditional solid waste management approach and will address the issue of waste in a productive manner generating income and building capacities for the most vulnerable population. Furthermore, the project is going to meet specific needs of the refugees by utilizing waste to produce items that they will choose as the most useful, such as blankets, buckets, chairs, torches, etc.
What are the expected outcomes?
The project will target refugee and host communities of low-income areas who are interested to become recycling entrepreneurs but require expert technical assistance and links with the global recycling industry to successfully set up their own plastic recycling business. Another outcome is to reduce the burden on the overloaded waste management system by removing recyclable plastic material from the waste stream and converting it into sellable products. A recycling plant can process around 3.2 tons of plastic per month.
Who are the project partners?
The proejct partners are UNHCR, Norwegian Geotechnical Institute (NGI), Movimiento Por La Paz (MPDL), Human Brights Engineering,
Precious Plastics.
Read more about the project here (fivemedia.com) and here (fastcompany.com).